
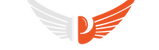
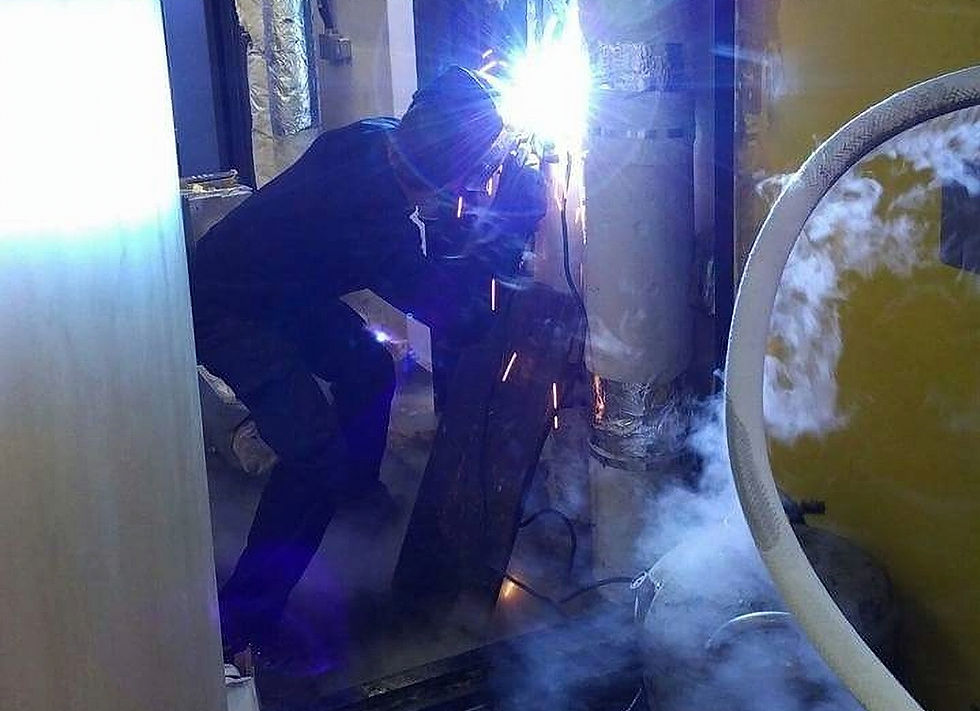


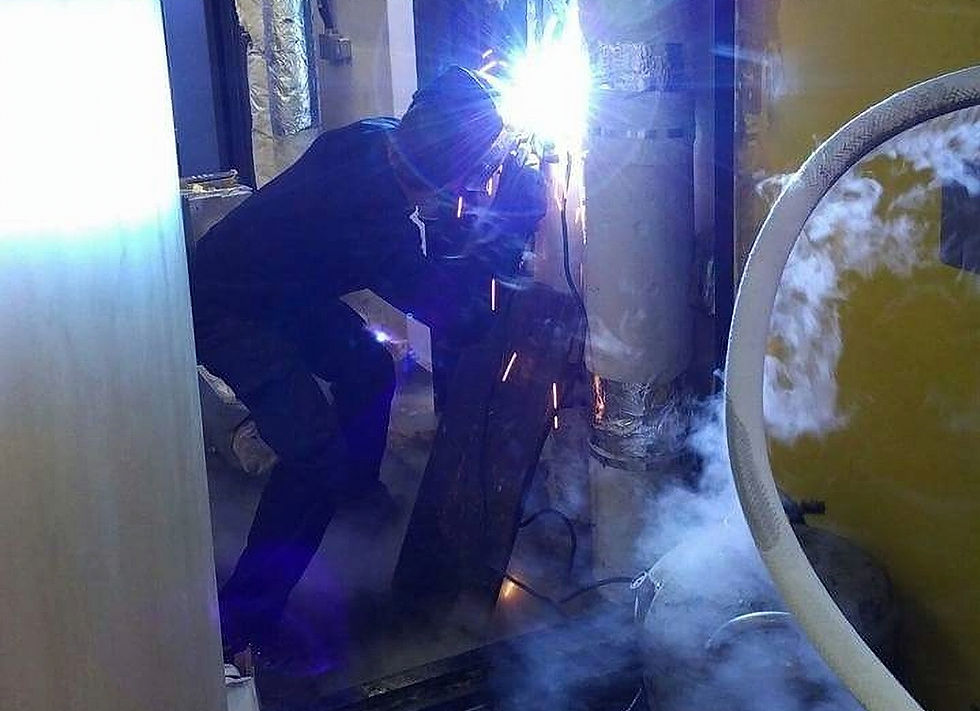
Pipework Fabrication
A major stainless steel pipework renewal project in Rushden, Northants
Tank Drain Pipework
We removed existing pipework and bracketry.
We fabricated pipework at the Precision Arc Engineering workshop. All pipework was purged with Argon high purity gas, to ensure clean internal welds and to avoid contamination.
We installed new 316 stainless steel 4inch pipework and lockable ball valve.
We pressure tested the new PAE pipework with nitrogen. The pressure test was witnessed and signed off. A test certificate was issued.
Tank Feed Pipework
We removed existing pipework and bracketry.
​
We fabricated pipework at the Precision Arc Engineering workshop. All pipework was purged with Argon high purity gas, to ensure clean internal welds and to avoid contamination.
PAE adapted the existing pipework to keep two tanks operational during the renewal project. Work commenced over a weekend to keep production going during the weekdays.
PAE installed new 316 stainless steel 2-inch pipework and valves to an agreed route.
We pressure tested the new PAE pipework with nitrogen. The pressure test was witnessed and signed off. A test certificate was issued.
Tank Overflow Pipework
We removed existing pipework and bracketry.
We fabricated pipework at the Precision Arc Engineering workshop. All pipework was purged with Argon high purity gas, to ensure clean internal welds and to avoid contamination.
We installed new 316 stainless steel 3” pipework to agreed route. Pipework from all 4 tanks was linked together in a common manifold and piped to 4 off IBCs.
We Installed the IBC manifold.
We pressure tested the new PAE pipework with nitrogen. The pressure test was witnessed and signed off. A test certificate was issued.
Tank Outlet Pipework
We removed existing pipework and bracketry.
We fabricated pipework at the Precision Arc Engineering workshop. All pipework was purged with Argon high purity gas, to ensure clean internal welds and to avoid contamination.
We Installed new 316 stainless steel 4” pipework to the agreed route. Pipework from all 4 tanks was linked together in a common manifold and piped to the filling pumps.
We pressure tested the new PAE pipework with nitrogen. The pressure test was witnessed and signed off. A test certificate was issued.
Tank Connecting Pipework
We removed existing pipework and bracketry.
We fabricated pipework at the Precision Arc Engineering workshop. All pipework was purged with Argon high purity gas, to ensure clean internal welds and to avoid contamination.
We Installed new 316 stainless steel 4” pipework and valves between the tanks, linking all 4 tanks to together.
We pressure tested the new PAE pipework with nitrogen. The pressure test was witnessed and signed off. A test certificate was issued.
Fill Station Pipework & Kiosk
We removed existing pipework and bracketry.
We fabricated pipework at the Precision Arc Engineering workshop. All pipework was purged with Argon high purity gas, to ensure clean internal welds and to avoid contamination.
We installed 2 new 316 stainless steel 4” pipework lines and valves to an agreed route.
We installed new fill GRP kiosk and internal pipework in agreed position.
We pressure tested the new PAE pipework with nitrogen. The pressure test was witnessed and signed off. A test certificate was issued.
You can see before and after photos of this pipework fabrication and installation project in the gallery above.